Der „Heilige Gral“ der Materialprüfung kostet nur ein paar Euro
Dauerfestigkeit schnell und kostengünstig bestimmen
Die „Dauerfestigkeit“ eines Materials zu ermitteln, ist bislang ein teures Unterfangen. Möchte etwa ein Stahlhersteller ermitteln, wie belastbar eine neue Legierung ist, muss er zehn Materialproben jeweils bis zu zehn Millionen Mal belasten. In der Folge können dann Entwicklungsingenieure den richtigen Stahl für ihr Produkt auswählen. Materialwissenschaftler der Universität des Saarlandes haben eine Methode publiziert, die diese Prüfung viel einfacher und günstiger macht.
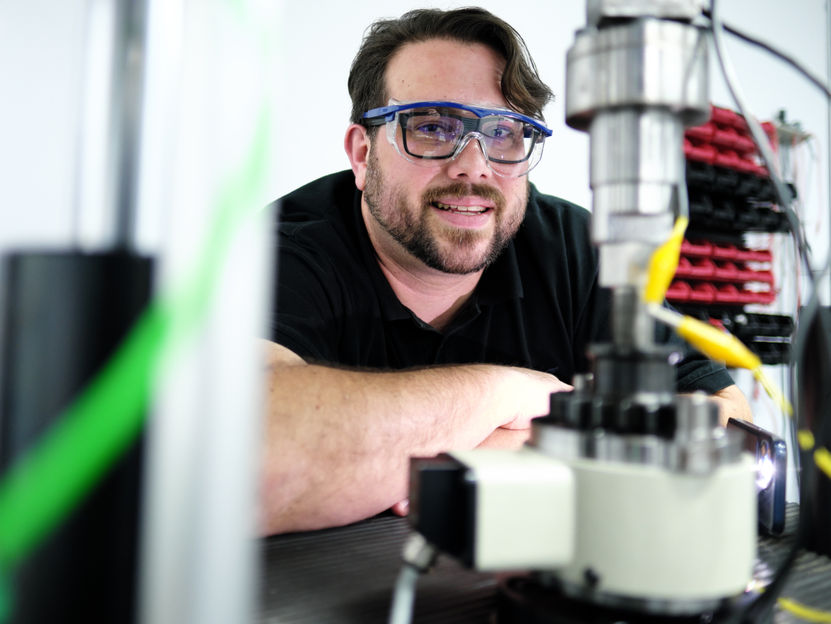
Dr. Florian Schäfer
© Thorsten Mohr
Es waren Bilder, die sich in das Gedächtnis vieler Menschen eingebrannt haben dürften: Das Trümmerfeld aus Zugteilen, die nach dem Zugunglück von Eschede 1998 über die Unfallstelle verstreut herumlagen. 101 Menschen starben beim bislang schwersten Zugunglück der deutschen Nachkriegsgeschichte. Verursacht hat das Unglück ein Rad, das aufgrund Materialermüdung gebrochen ist. Das Unglück macht auf schreckliche Weise klar, wie wichtig ein ausgereiftes Verfahren ist, um die Belastbarkeit eines Materials zu prüfen.
In der Werkstoffprüfung läuft das im Allgemeinen so: Eine Materialprobe, beispielsweise eine neu entwickelte Stahl-Legierung, wird im Prüflabor zwei bis zehn Millionen Mal mit einer definierten Kraft be- und wieder entlastet. Das Ganze wird dann an mindestens 10 Proben, besser mehr, wiederholt, und am Ende erhalten die Werkstoffprüfer einen Wert, der die Grenze definiert, ab der ein Material unsicher wird. Vereinfacht ausgedrückt, wird dann klar, ob eine Brücke, die mit diesem Stahl errichtet wird, einen Lkw mit 15 Tonnen nach Jahren auch noch sicher tragen kann, den 20-Tonner aber nicht mehr sicher.
„Dieses Verfahren ist aber sehr teuer“, erläutert Dr. Florian Schäfer, Werkstoffwissenschaftler an der Universität des Saarlandes. Gemeinsam mit Masterstudent Jan Rosar hat er eine Jahrzehnte alte Methode aufs Neue untersucht, die nicht 1.000 Euro pro Tag und Probe wie die klassische Materialprüfung kostet. Sie haben ein Verfahren untersucht, die „quantitative Thermometrie“. Dabei wird die Temperaturveränderung gemessen, die ein Material während der Be- und Entlastung erfährt. Über diese Methode kann man auch die Dauerfestigkeit eines Materials statt mit vielen Proben mit nur einer Messung abschätzen.
Die Methode hatte allerdings in der Wissenschaft keinen großen Widerhall gefunden. Ihr Entwickler war jahrzehntelang in der Industrie tätig und hat wissenschaftlich kaum publiziert, so dass bisher das komplizierte und teure so genannte Wöhlerverfahren seit 1871 wie eingangs beschrieben der wissenschaftliche Goldstandard ist. „Wenn man bedenkt, dass unser Aufbau mit billigen Sensoren aus Rauchmeldern gerade einmal 114 Euro gekostet hat und mit der einfachen Messung einer einzigen Probe dasselbe Ergebnis erzielt, könnte sich das allerdings ändern“, erläutert Florian Schäfer.
Im Kern können er und Jan Rosar mit diesen billigsten Mitteln anhand der Temperaturentwicklung in der Stahlprobe ergründen, was auf atomarer Ebene im Material geschieht und so die Dauerfestigkeit ebenso genau bestimmen wie mit gängigeren Methoden zur Temperaturermittlung. „Dazu dienen heute in der Regel Infrarotkameras, die Temperaturunterschiede sichtbar machen können. Diese sind mit einer Auflösung von einem Millikelvin allerdings viel weniger leistungsfähig als wir mit unseren Billigsensoren.“ Mit diesen können sich Temperaturunterschiede von einem Tausendstel Millikelvin darstellen lassen, so Florian Schäfer.
Die Methode wurde 1982 von Dr. Klaus Stärk an der Materiaprüfanstalt in Stuttgart erstmals erprobt, litt aber an der damals noch schlechteren Messtechnik. „Wir haben eine 40 Jahre alte Messprobe in den Versuchsaufbau eingespannt und die Veränderung unter Ermüdungsbelastung gemessen“, erläutert Florian Schäfer das Vorgehen. „Abends hatten wir die perfekte Messkurve. Das konnten wir anfangs selbst nicht glauben“, gibt er zu. „Aber wir haben dann, im Gegensatz zu den alten Arbeiten, noch viele andere Werkstoffe durchgezogen und kamen immer zu dem gleichen Ergebnis: Die Genauigkeit der Werkstoffprüfung war überragend“, erläutert der Wissenschaftler.
Damit haben sie den „Heiligen Gral der Materialprüfung“, wie Florian Schäfer die Bestimmung der Dauerfestigkeit augenzwinkernd nennt, deutlich günstiger gemacht. Wenn sich das Verfahren einmal tatsächlich industriell in großem Maßstab ausrollen lassen sollte, könnte dies eine Grundlage sein, Brücken, Fahrzeuge und tausende weitere Produkte zu bauen, deren Festigkeit mit annähernd hundertprozentiger Sicherheit für eine lange Zeit garantiert werden kann. Schlimme Unglücke wie das Zugunglück von Eschede wären damit zwar noch immer nicht vollständig ausgeschlossen. Aber sie wären um ein Vielfaches unwahrscheinlicher, schlicht, weil das Verfahren, mit dem die Belastungsgrenzen eines Werkstoffes bestimmt werden kann, erheblich günstiger und schneller zu durchlaufen wäre. Dann bleibt mehr Zeit für die Weiterentwicklung der Materialien.
Originalveröffentlichung
Schaefer, F., Rosar, J., Wu, H., Starke, P., & Marx, M. (2022). Obtaining a lower estimate of the fatigue limit of metals by a simplified quantitative thermometric approach in a low-cost one-specimen test. International Journal of Fatigue, 159, 106729
Schäfer, F., Rosar, J., Marx, M., Herter, F., Wu, H., & Starke, P. (2022). Quantitative Thermometry: A Revived Simplified Approach to Fatigue Strength Determination and Deformation Mechanisms. Procedia Structural Integrity, 37, 299-306