Environmentally Friendly Catalyst Drastically Reduces Laughing Gas Emissions
A catalyst that reduces the emission of a nitrogen-containing greenhouse gas by more than 90%, a sensor system that continuously measures the temperature of liquid steel and consequently contributes significantly to improving quality, and a solder paste that makes it possible for electronics manufacturers to assemble circuit boards without resin or other residues: these are the praiseworthy developments that have been awarded the 2005 Heraeus Innovation Prize. What all three innovations have in common is that they can be integrated in users' existing systems without requiring extensive retrofitting and investments.
The first prize endowed by the Heraeus concern carries a EUR 2,500 award and was presented to Dr. Uwe Jantsch of W. C. Heraeus for the "Multiphase catalyst for the selective elimination of N2O". The production of fertilizers in the chemical industry (ammonia combustion process) requires large quantities of catalysts made of platinum alloys. The catalysts are used in the form of knitted gauzes with diameters as large as six meters. An unwanted byproduct of the ammonia combustion process is ozone damaging laughing gas (N2O), a greenhouse gas that is 310 times as powerful as carbon dioxide. The research team of Dr. Uwe Jantsch developed an innovative multiphase catalyst that makes it possible to significantly reduce laughing gas before it even forms in ammonia combustion. But one of the most important elements in the innovation is a downstream secondary catalyst that selectively destroys laughing gas when it is formed. In combination with the platinum gauzes directly above it, the emission of the greenhouse gas is reduced by more than 90%. Since some 1.2 million tons of laughing gas are emitted in the production of fertilizers each year, the Heraeus innovation represents a major step forward for the environment. The new development has been very well received in the market since it helps manufacturers comply with the internationally enforced emission limits for laughing gas (Kyoto Protocol).
The second prize went to Martin Kendall of Heraeus Electro-Nite for the "Through wall sensor". In state-of-the-art continuous casting production processes for steel production, everything depends on maintaining exact temperature ranges around 1,550 °C while the casting is carried out. In the past, temperature control was usually accomplished using optical analyses. The CasTempTM sensor measurement system developed by Martin Kendall and an international team at Heraeus Electro-Nite makes it possible for steel manufacturers to directly and continuously measure the temperature of the liquid steel in this production step. This means they can respond immediately if the temperature drops below a critical point where the steel cools. The advantages for the steel industry in comparison to optical testing methods are higher process reliability, improved steel quality, reduced energy costs, and less waste as a result of prematurely "cooled" steel.
The third prize went to Wolfgang Schmitt of W. C. Heraeus for solder pastes with resin- and residue-free fluxes. A fundamental and very old problem related to the use of solder pastes for the assembly of circuit boards has been resolved with an innovation developed by Wolfgang Schmitt and the SMT Materials team. The new solder paste gel is a chemical system that electronics manufacturers such as circuit board assemblers can now use to solder components to tracks made of tin or other metals without the interference of resin and flux residues. Usually, solder powder (containing tin, for example) is mixed with a flux (a resinous medium) to form a solder paste. After the assembly is completed, a resinous residue generally remains and has to be removed in a time-consuming process. The new solder paste from Heraeus reduces flux residue from 3.5 to 0.2 percent by weight. This not only eliminates cleaning costs; the gel also improves the quality of the circuit boards and contacts on electronic components in general.
Topics
Organizations
Other news from the department research and development
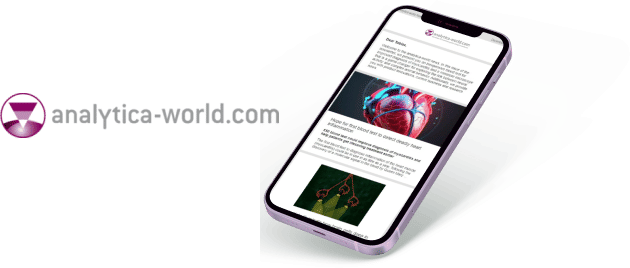
Get the analytics and lab tech industry in your inbox
By submitting this form you agree that LUMITOS AG will send you the newsletter(s) selected above by email. Your data will not be passed on to third parties. Your data will be stored and processed in accordance with our data protection regulations. LUMITOS may contact you by email for the purpose of advertising or market and opinion surveys. You can revoke your consent at any time without giving reasons to LUMITOS AG, Ernst-Augustin-Str. 2, 12489 Berlin, Germany or by e-mail at revoke@lumitos.com with effect for the future. In addition, each email contains a link to unsubscribe from the corresponding newsletter.