High-energy X-rays give industry affordable way to optimize cast iron
Cast iron can be modified through the manufacturing process to optimize its mechanical and physical properties, such as strength and durability.
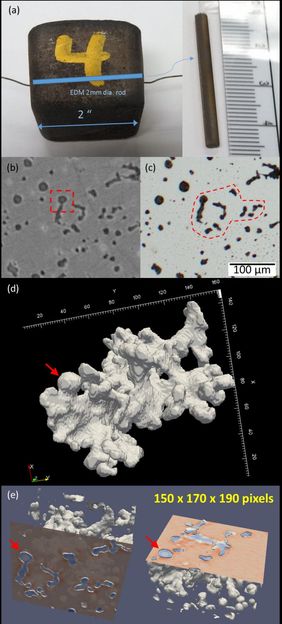
(a) The 2-inch casting block and a 2 mm diameter rod that is electrical discharge machining (EDM) cut out of the sample. (b) A typical slice of tomographic image obtained in the present study. (c) An un-etched metallography image of the same region in (b) under optical microscope (OM). (d) The reconstructed 3-D model of the graphite particles in (b). It shows that the 2-D features observed in (b and c) belong to a coral tree-like structure with flat, rounded branches that span ?200 μm in the iron matrix. (e) The left is the slicing surface and the graphite structure beneath the surface. The right side is the same CG structure but sliced in a different orientation. It shows the same feature (red arrow) could be identified as either nodular graphite (NG) or compact graphite (CG) in 2-D analysis depending on where one slices it.
Scripta Materialia
But the manufacturing process is as much art as science, producing good results yet not capturing cast iron's full potential. Controversy still exists over the correlation between manufacturing casting parameters and desirable properties. Limited by typical industrial 2-D imaging techniques or time-consuming 3-D laboratory studies, researchers have been unable to pinpoint the exact processing parameters needed to elicit the ideal properties for each cast iron application.
Finding an easier way to peer deep inside the alloy to get a definitive answer could be a boon for consumers as well as give the U.S. industry a competitive advantage. According to a study high-energy synchrotron X-rays can provide that insight.
"By understanding the structure, it will be possible to develop alloys with improved mechanical and thermal properties. This implies that for applications, such as vehicle engine and engine components, one could use less material and reduce overall vehicle weight that would translate into fuel savings," said Dileep Singh, Group Leader of Thermal-Mechanical Research at Argonne National Laboratory's Center for Transportation Research and the technical lead of this study at Argonne.
For the transportation industry, the ability to modify manufacturing processes to create high-performance materials could aid in the development of more fuel-efficient engines or engine parts that can withstand heat better to have longer lifespans.
"Researchers at Caterpillar are actively seeking to improve our understanding of cast iron alloys in order to provide innovative product solutions to our customers," said Richard Huff, a Technical Team Leader with Caterpillar Inc., which supplied engine alloy castings for use in the proof of principle study.
The study results showed that high-energy X-ray tomography can reveal previously unknown behaviors of graphite in cast iron, such as the growth of nodules, as it undergoes various treatments. The X-rays also can unambiguously classify the particle type involved in the behavior, which is critical to identifying the structure-process relationship. These insights hold the key to manipulating the atomic structure of the graphite through manufacturing treatments such as changing the chemistry of the melt and altering the inoculants added to the liquid cast iron.
Synchrotron X-ray analysis has several advantages over the current techniques used to evaluate graphite microstructure.
Three-dimensional imaging of the structure of graphite, its spatial arrangement in the alloy, and its phase connectivity, are key factors that determine the properties of cast iron. These parameters cannot be attained reliably by the current industry standard 2-D test. Less frequently used, but more effective is the use of focused ion beams (FIB) and transmission electron microscopy, which can provide high-resolution 3-D images, but is labor-intensive, time consuming and destroys the sample. High-energy X-rays penetrate inhomogeneous samples up to a centimeter thick under real operating conditions. This avoids the challenges of FIB and TEM techniques while also providing a better statistical representation of parameters in bulk material.
The research team found that the synchrotron characterization methods enable new insight into why compacted graphite iron, which is used by Caterpillar in heavy-duty engine components, can conduct heat better than ductile iron while maintaining good ductile strength. The answer lay in the shape, size, and distribution of the graphite particles in the cast iron.
"The 3-D characterization of the material enables greater insight into the structure formation and structure-property relationships," Huff said.