Research into Gas Detection in the Workplace Reveals Lack of Confidence in Gas-Monitoring Set-ups
The findings of industry-wide research into gas detection in the workplace were announced, revealing a number of alarming gas safety concerns. The research demonstrated the lack of confidence in their current gas detection systems amongst the higher level within an organisation – only 32% of managers are very confident that the gas detectors in their workplace actually work. Additionally, despite the fact that frequency of gas detectors testing was ranked as the most important factor in ensuring workplace safety, only two in five managers believe that their gas detectors are not tested regularly enough. The research therefore reveals a lack of consistency regarding what constitutes a reliable gas detection set-up. The full findings from the research are published in a white paper.
The research, carried out by third party researchers, was commissioned by the specialist electrochemical-sensor manufacturer Analytical Technology Inc (ATI) in response to expressed concerns in the water/utility industry about methods of safe gas detection. A total of 100 people were interviewed working in six different industries, namely food and beverage manufacturing, pharmaceutical manufacturing, petrochemical, water/utility, metal plating/printed circuit board manufacturing and healthcare. Within these industries the employees interviewed were from a range of job titles at managerial level (plant and facility managers, project managers and health and safety managers) and at workforce level (factory/shop floor workers, engineers, machine operators, instrument technicians/engineers and service engineers).
The research focuses on three main areas of interest – current awareness and concerns around gas detection, the purchasing of gas detectors and factors influencing it, and the testing of gas detectors. Managerial staff and their workforce express different opinions across a number of important issues. When asked about the procedure if all the gas detectors in a plant failed, alarmingly almost a quarter of managers would carry on as normal. In stark contrast, only 8% of their workforce would continue in the potentially dangerous working environment. While 80% of factory/plant workers are concerned about the risks that gas poses in their workplace, they are in many cases unaware if there are gas detectors in place to ensure their safety. This highlights a clear need for procedures to be put in place to enable protection of workforces and compliance with industry regulations.
The AutoTest function, which automatically checks that a gas detector is working correctly, has been identified as a necessary characteristic of a reliable gas detection set-up, and 89% of those currently working with AutoTest detectors in place claim that they would never use a system without this function. Gas detector testing differs dramatically from company to company due to the lack of explicit regulation in this area and although frequent gas detection is proven to improve confidence in gas detection set-ups, around one in eight managers manually test their detectors less frequently than annually.
Most read news
Organizations
Related link
Other news from the department business & finance
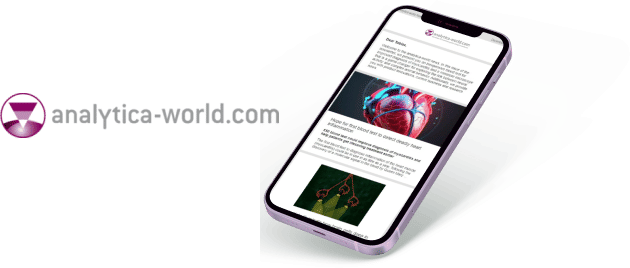
Get the analytics and lab tech industry in your inbox
By submitting this form you agree that LUMITOS AG will send you the newsletter(s) selected above by email. Your data will not be passed on to third parties. Your data will be stored and processed in accordance with our data protection regulations. LUMITOS may contact you by email for the purpose of advertising or market and opinion surveys. You can revoke your consent at any time without giving reasons to LUMITOS AG, Ernst-Augustin-Str. 2, 12489 Berlin, Germany or by e-mail at revoke@lumitos.com with effect for the future. In addition, each email contains a link to unsubscribe from the corresponding newsletter.